Returns have increased in frequency with the development of e-commerce and are worth almost a trillion dollars globally each year. Compared to at least 30% of items ordered online, less than 10% of in-store purchases are returned. Smart businesses employ reverse logistics to increase client retention and repeat business operations while reducing return-related losses.
Reverse logistics is a crucial component of supply chain management that successful supply chain companies use to carry out operations effectively and boost value for their end customers. Organizations use reverse logistics when goods return from their destination back through the supply chain to the seller and possibly back to the suppliers through processes like returns or recycling.
Successful reverse logistics aims to maintain product circularity so that production, distribution, shipping, delivery, returns, repairs, and disposal may all continue to line up as parts of an efficiency model that is always spinning. This process does not only cut costs for businesses, and subsequently for their clients and end users, but it also lessens the number of things that wind up in our landfills. Your company may provide value for its clients by demonstrating how it manages these necessary procedures by creating and implementing a strong reverse logistics plan.
Optimized reverse logistics also leads to better supply chain visibility, which leads to benefits like:
- Cost reduction
- Greater customer satisfaction
- Better customer retention
- Faster and better service
- Loss reduction
- Improved brand sentiment
- Waste reduction and greater sustainability
Understanding the various types of reverse logistics helps you implement efficient processes and reduce costs.
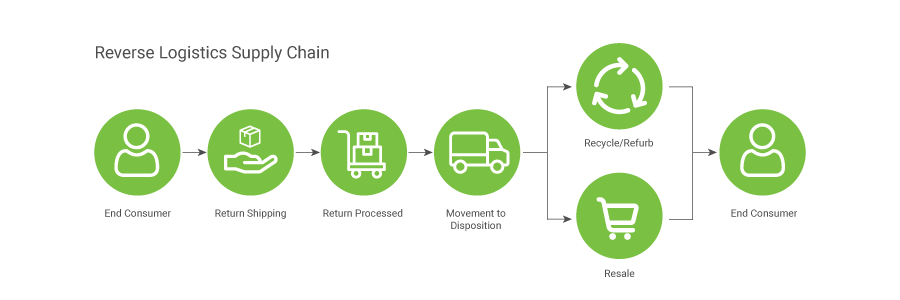
Traditional Logistics Versus Reverse Logistics
A traditional logistics process flow begins at the supplier, to the factory, distributor, retailers, and ends with customers. Reverse logistics follows the same process backward: begins at the customer and moves counterclockwise to return goods to any location along the supply chain.
Well-planned supply chains can handle some requirements for reverse logistics and are adaptable to changes. Products can be returned using this process either to the original supplier or one step further down the supply chain. Even regular sales or discount channels (like liquidators) can receive returned goods.
Forward and Reverse Logistics Process
In the image below you can follow the traditional logistics process as a straight line and the reverse logistics process as a dashed line.
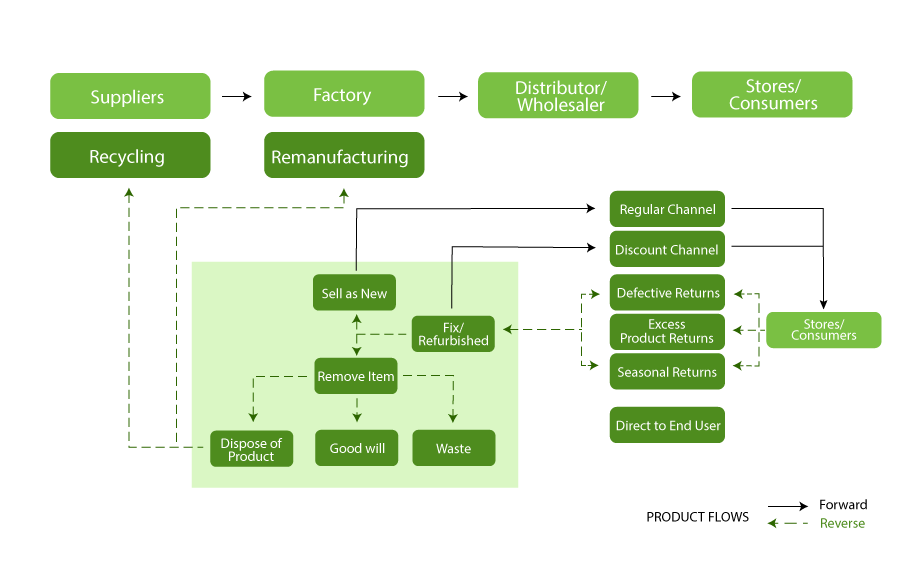
Types of reverse logistics
Returns management
The most typical reverse logistics procedure for handling routine customer returns is returns management, which should provide a seamless, trouble-free experience to increase customer loyalty and brand image.
Return policy and procedures
All customer returns are evaluated in accordance with this policy, which should be consistently upheld by both clients and staff. It’s best to maintain these policies out in the open and simple for customers to access.
Remanufacturing or refurbishment
Reconditioning returned goods avoids businesses and merchants from forgoing profit (or losing money) on flawed goods while reducing unnecessary waste.
Packaging management
In order to cut waste and save money on new packaging for returned items, businesses using package management procedures are able to reuse packaging.
Unsold products
The process of returning unsold products to manufacturers is specifically focused on sending items from end-users or fulfillment centers back to the producers. Delivery rejection, weak sales, or other causes may be involved.
End of service life
When a product reaches the end of its useful life, some must be returned to the manufacturer to properly handle their environmental disposal.
Delivery failure
Products that cannot be delivered are usually sent back to the manufacturer from fulfillment centers, however, efficient businesses may be able to handle delivery failure by fixing the problem and resending the product.
Rental equipment
Products that are rented or leased are returned to the manufacturer at the end of a certain term for disposal, recycling, or redeployment.
Repair and maintenance
Products such as consumer electronics (laptops, for example) may be returned to have repairs or warranty work performed.
Strategies to Optimize Reverse Logistics
Cohesive solutions that take into account speed, efficiency, and cost are required for businesses to maximize reverse logistics. Think about policies, partners, data, capacity, logistics, and transportation before acting. Try the following strategies to improve your reverse logistics:
- Review and revise the procedures related to your company’s returns and repairs.
- Collaborate closely with suppliers to ensure a smooth, integrated experience for customers.
- Use data collected on product returns to optimize processes in sales, product design, and forward logistics processes.
- Track products forward and backward so you can easily identify outlier data and selectively recall products instead of entire lines.
- Centralize return centers to efficiently determine how best to reclaim product value
- Regularly review the processes for forward and reverse logistics and transportation to determine where they intersect and save time, money, and trips.
- By using cloud-based logistics software solutions, such as Planograma you can track asset recovery, manage refurbishment, and provide business intelligence analytics.